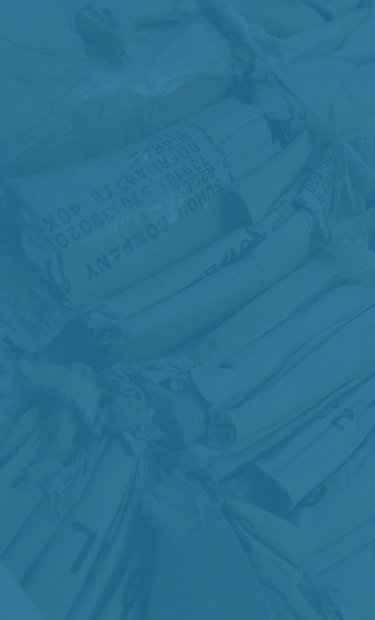
Hydraulic and pneumatic balers – Learn the differences!
Read along to learn the differences between a hydraulic and a pneumatic baler.
Pneumatic and hydraulic balers – both for recycling
One of the decisions you’ll have to make when deciding to install a recycling baler on your company’s property is between hydraulic and pneumatic balers.
Compressing recyclable materials like paper, cardboard, and plastic into thick blocks (bales) that can be readily moved and recycled is essentially what both of these kinds of machines do.
Both devices have a power source and press materials using that power.
What then distinguishes them?
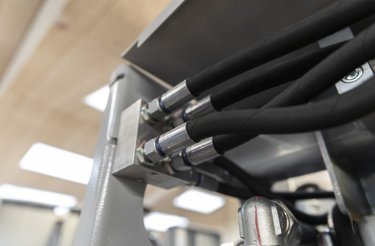
Pneumatic balers characteristics
Compressed air powers pneumatic balers. The upper cylinder is filled with air, which exerts pressure that causes the pressing plate to descend. Without the need for additional power, the pressure locks the pressing plate into place.
There are no electrical components in pneumatic balers; they only operate on compressed air.
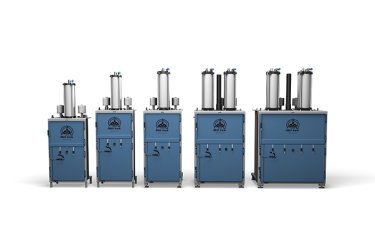
Hydraulic balers characteristics
Electric motors are used by hydraulic balers to pump hydraulic oil. The hydraulic oil causes the rams to exert pressure, which lowers the pressing plate.
Hydraulic balers are more powerful than pneumatic balers, and make more dense bales.

“Pneumatic Balers use air to depress the pressing plate, whereas Hydraulic Balers use hydraulic oil to operate the pressing plate through powerful pressing rams”
Pneumatic vs. hydraulic balers: Additional factors to consider
These two different types of balers might assist your company in effectively managing waste. Each has advantages that are more suitable for a specific type of organization. Typically, it depends on the unique requirements of an organization.
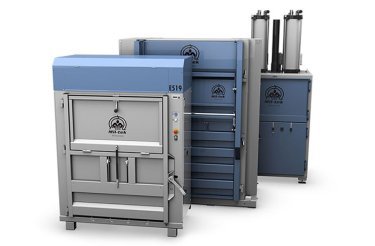
Differences between hydraulic and pneumatic balers
- Volume – Hydraulic balers work well for high volumes (approx more than one ton per week)
- Size – Pneumatic balers are typically smaller and better suited to work spaces with limited space
- Noise – Hydraulic balers are often quite noisy and are therefore often installed away from the production process
- Noise – Because hydraulic balers can be fairly noisy, they are frequently positioned outside of the manufacturing area
- Maintenance – Both hydraulic and pneumatic balers need regular maintenance, while pneumatic balers need less because they don’t have any electrical components
- Power Source – Pneumatic balers can be powered by plugging directly into existing air lines. If not, a modest compressor is needed
- Power – A pneumatic baler uses pressurized air to lock in position the pressing plate once it has been lowered. In order to maintain continuous pressure, hydraulic balers need continual power
- Hygiene – Due to their reduced risk of contamination, pneumatic balers are more suitable for use in food manufacturing facilities
Have a question?
Get in touch today to learn more about how Mil-tek can help your business save time, space and money by better handling waste.